What is Porosity in Welding: Key Elements and Their Effect On Weld High Quality
Wiki Article
Unwinding the Enigma of Porosity in Welding: Tips for Decreasing Defects and Making The Most Of Quality
In the elaborate world of welding, porosity stays a relentless challenge that can significantly impact the high quality and stability of bonded joints. As we delve right into the midsts of porosity in welding, discovering the secrets to its prevention and control will certainly be vital for specialists looking for to grasp the art of top notch weldments.Comprehending Porosity in Welding
Porosity in welding, a common issue come across by welders, refers to the visibility of gas pockets or spaces in the welded product, which can jeopardize the stability and quality of the weld. These gas pockets are commonly entraped throughout the welding process because of numerous factors such as incorrect securing gas, infected base materials, or inaccurate welding criteria. The development of porosity can weaken the weld, making it vulnerable to splitting and rust, inevitably bring about structural failures.Recognizing the source of porosity is vital for welders to properly avoid its incident. By acknowledging the value of preserving proper gas shielding, guaranteeing the tidiness of base materials, and enhancing welding settings, welders can considerably decrease the likelihood of porosity development. Furthermore, utilizing methods like preheating the base product, utilizing appropriate welding techniques, and conducting comprehensive inspections post-welding can better assist in reducing porosity issues. Overall, a detailed understanding of porosity in welding is essential for welders to generate top quality and long lasting welds.
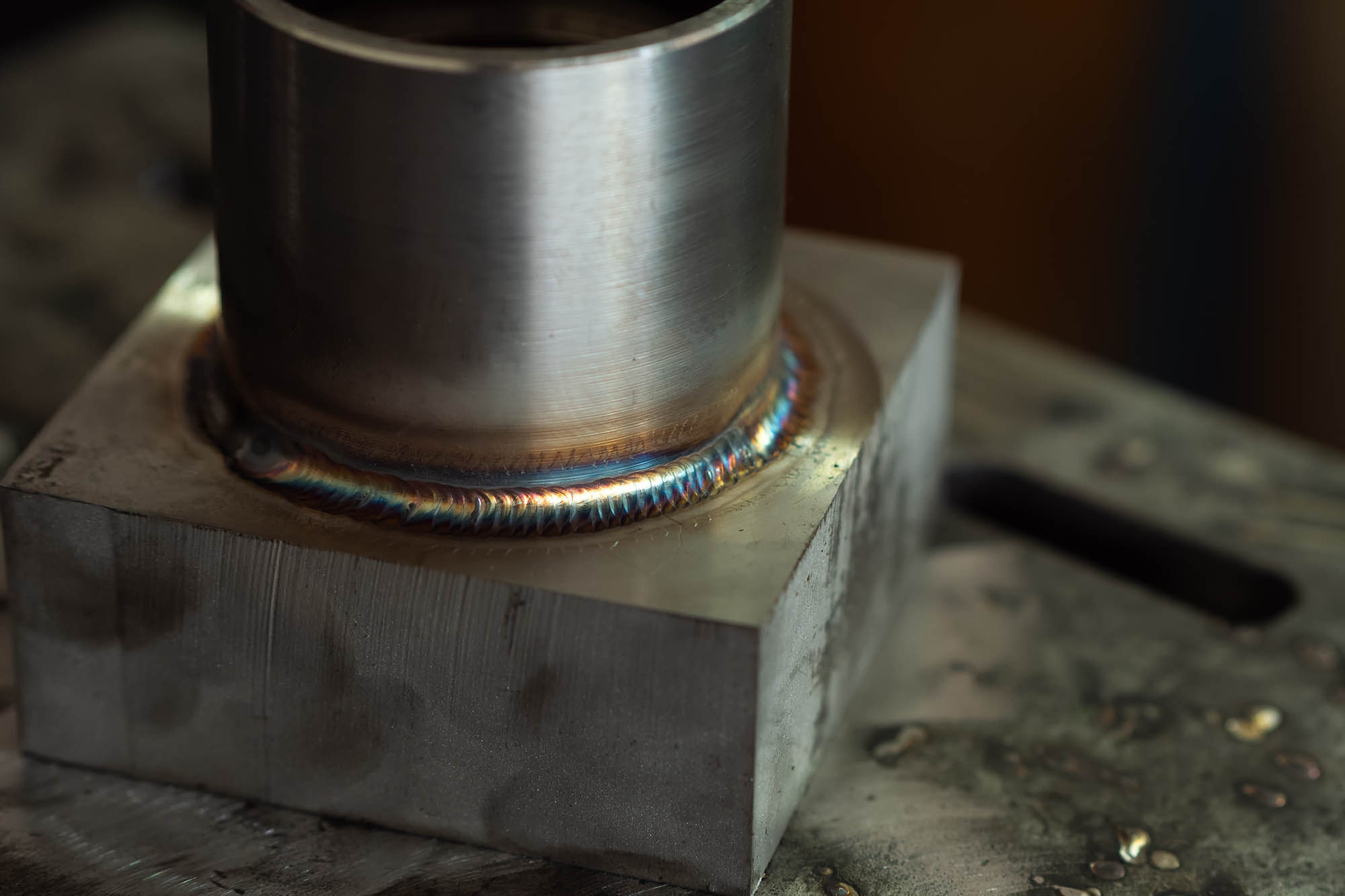
Usual Sources Of Porosity
When checking welding procedures for possible top quality concerns, comprehending the usual causes of porosity is vital for preserving weld stability and preventing structural failures. Porosity, characterized by the existence of cavities or gaps in the weld steel, can dramatically jeopardize the mechanical residential or commercial properties of a bonded joint.
In addition, welding at inappropriate specifications, such as exceedingly high traveling rates or currents, can produce excessive turbulence in the weld swimming pool, capturing gases and creating porosity. By attending to these common reasons through appropriate gas securing, product prep work, and adherence to ideal welding specifications, welders can decrease porosity and boost the quality of their welds.
Techniques for Porosity Prevention
Applying effective precautionary actions is important in minimizing the event of porosity in welding processes. One strategy for porosity avoidance is making sure proper cleansing of the base metal prior to welding. Impurities such as oil, oil, rust, and paint can lead to porosity, so complete cleansing using appropriate solvents or mechanical approaches is essential.
Making use of high-quality filler products and shielding gases that are appropriate for the base metal and welding procedure can considerably minimize the danger of porosity. Additionally, preserving proper welding specifications, such as voltage, current, take a trip rate, and gas circulation rate, is important for porosity avoidance.
Furthermore, utilizing proper welding methods, such as preserving a constant travel speed, electrode angle, and arc length, can aid prevent porosity (What is Porosity). Appropriate training of welders to guarantee they adhere to ideal techniques and quality assurance procedures is also crucial in minimizing porosity check my reference defects in welding

Ideal Practices for Quality Welds
Guaranteeing adherence to market requirements and proper weld joint preparation are basic aspects of achieving regularly top quality welds. In enhancement to these foundational steps, there are numerous best methods that welders can carry out to additionally improve the quality of their welds. One trick technique is preserving appropriate cleanliness in the welding location. Contaminants such as oil, oil, rust, and paint can detrimentally affect the top quality of the weld, causing defects. Completely cleaning up the workpiece and bordering area prior to welding can help mitigate these concerns.Another best technique is to very carefully select the suitable welding criteria for the certain materials being signed up with. This includes setting the right voltage, current, travel speed, and securing gas circulation price. Proper parameter option guarantees optimum weld penetration, combination, and total quality. In addition, using high-quality welding consumables, such as electrodes and filler metals, can substantially impact the final weld why not try this out quality. Purchasing costs consumables can result in stronger, a lot more sturdy welds with fewer problems. By adhering to these best methods, welders can continually produce top quality welds that satisfy sector criteria and exceed customer expectations.
Importance of Porosity Control
Porosity control plays an important function in guaranteeing the stability and high quality of welding joints. Porosity, characterized by the presence of dental caries or spaces within the weld metal, can dramatically endanger the mechanical properties and structural honesty of the weld. Too much porosity deteriorates the weld, making it much more at risk to splitting, corrosion, and total failure under functional lots.Effective porosity control is crucial for preserving the wanted mechanical homes, such as toughness, ductility, and strength, of the bonded joint. What is Porosity. By decreasing porosity, welders can enhance the general top quality and dependability of the weld, making sure that it meets the performance demands of the desired application
Additionally, porosity control is crucial for attaining the preferred visual look of the weld. Excessive porosity not only deteriorates the weld yet also diminishes its visual charm, which can be essential in industries where looks are essential. Proper porosity control methods, such as utilizing the right securing gas, regulating the welding parameters, and guaranteeing appropriate sanitation of the base products, are crucial for producing top quality welds with very little problems.
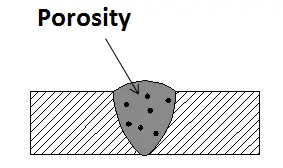
Verdict
Finally, porosity in welding is a common problem that can jeopardize the high quality of the weld. By comprehending the reasons for porosity and carrying out correct avoidance strategies, welders can minimize defects and achieve better welds. It is essential to control porosity in welding to ensure the integrity and toughness of the last item. Carrying out click now best techniques for porosity control is crucial for achieving optimum welding outcomes.Report this wiki page